Shorter is Better: How Electra Optimizes eSTOL Aircraft Design with Rapid CFD
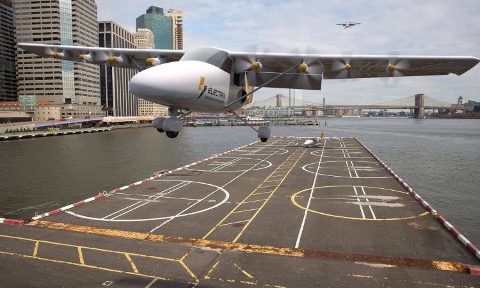
For a long time, science fiction movies have imagined aircraft navigating through skyscrapers in a bustling modern city. However, the reality is that cities lack runways for aircraft, and helicopters are too loud and inefficient for mass-market transportation. This is where Electra’s electric Short Take-Off and Landing (eSTOL) aircraft comes in.
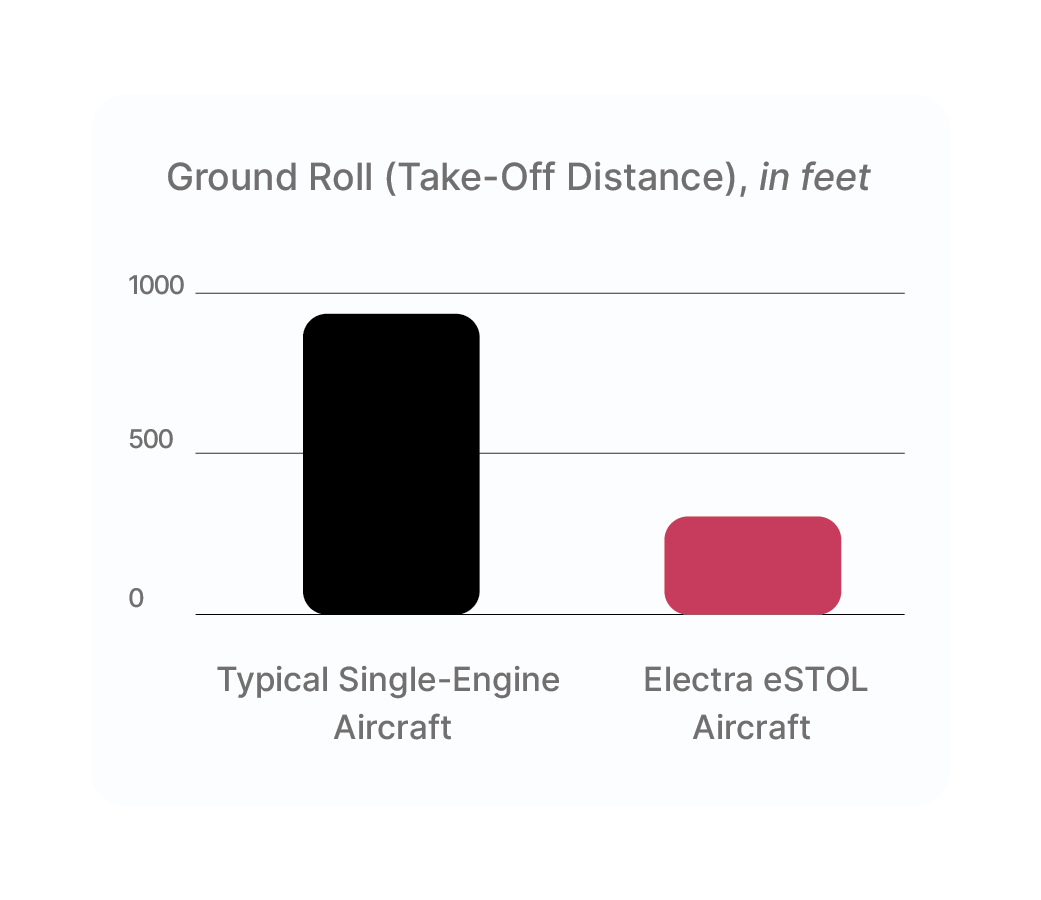
By mounting an array of propellers along the aircraft’s wingspan, Electra can achieve short take-off from urban rooftops and parking garages. These propellers are uniquely designed and positioned to create high speed airflow blowing toward the wings, which can generate extra lift force to allow the airplane to take off in a short distance. For such an innovative design, there is a lack of empirical design rules for engineers to draw from. Engineers must rely on computational fluid dynamics (CFD) simulation to design.
The challenge is the enormous design space; the size, position, and number of propellers and wings, their interaction with control surfaces, etc. There are tens of configurations that all must be simulated in each of various operating scenarios, like take-off, landing, transition, loiter, and more. And each operating scenario must be mixed with environmental effects and different performance conditions, like how much weight the aircraft is carrying or whether urgency or efficiency is the priority. Electra was quickly facing thousands of simulations to inform its overall aircraft design. What’s even more challenging is that, as a startup, Electra needs to finalize a design within a very short period.
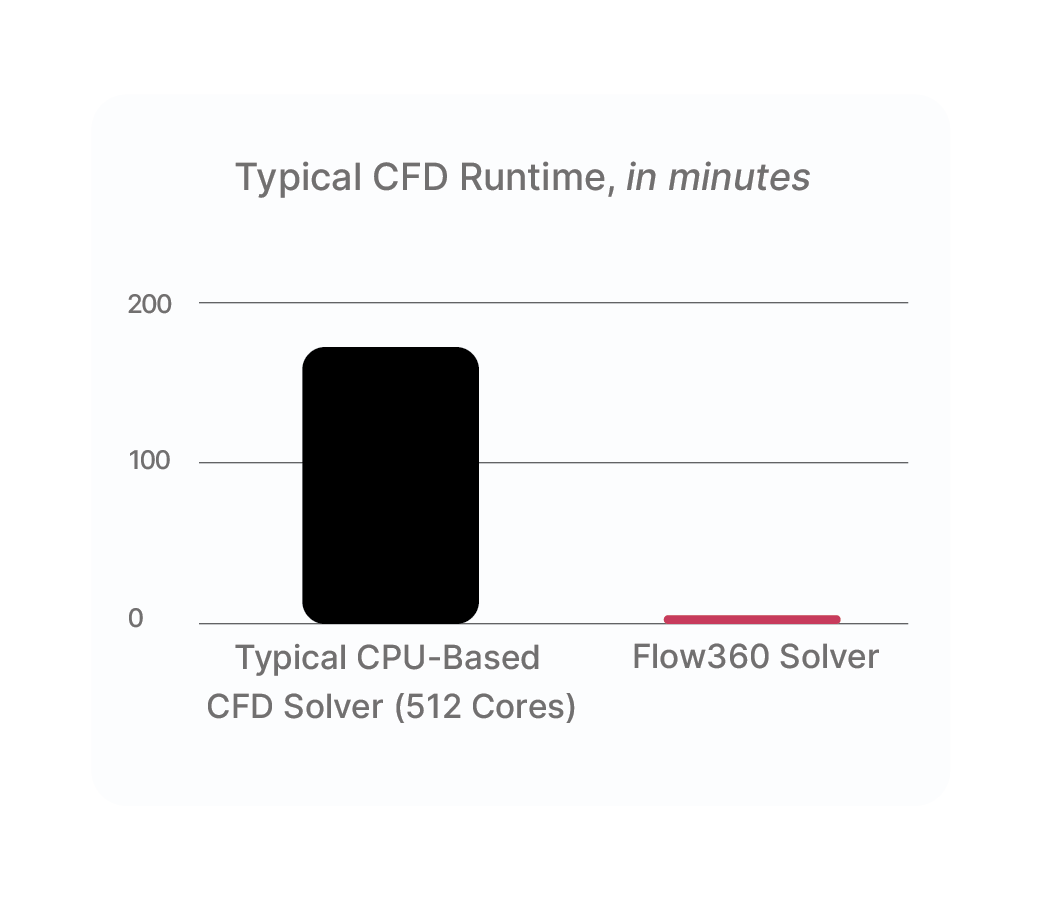
Flow360 is fast, built from the ground up for emerging computing chips, such as GPUs. Simulations that once required 3 hours to run now only require 5 minutes with this solver. Flow360 is reliable, built specifically for high-end CFD applications in aerospace and automotive, nor does it sacrifice accuracy for speed. Running Flow360 is easy, with an option to run in the cloud. Without having to maintain any computing hardware, this solver saves the Electra team hundreds of thousands of dollars.
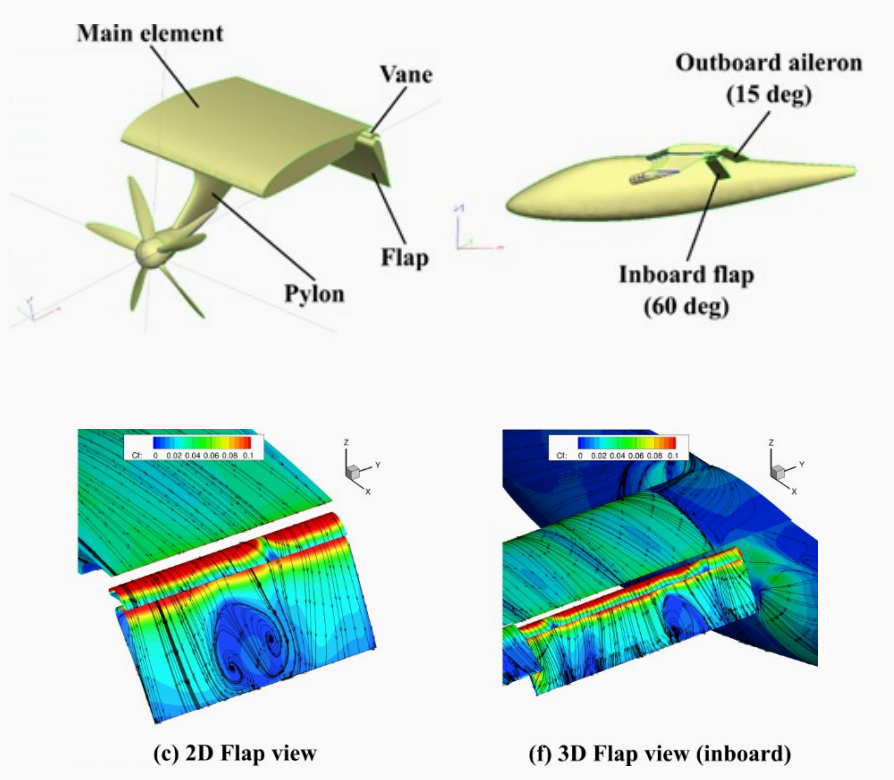
Even though Electra has some of the world’s most renowned aerodynamicists with decades of experience working with nearly all CFD tools, they quickly recognized that none of existing CFD tools can deliver the speed, accuracy, and cost that are required to get the job. Not until they found Flow360.
Thanks to the fast design iteration enabled by Flow360, Electra converged on an initial aircraft design within three months, which would have otherwise taken up to 12 months. Saving 9 months as a result sped up Electra’s path to market, which is time worth at least tens of millions of dollars to a company that is addressing an emerging market worth hundreds of billions dollars.
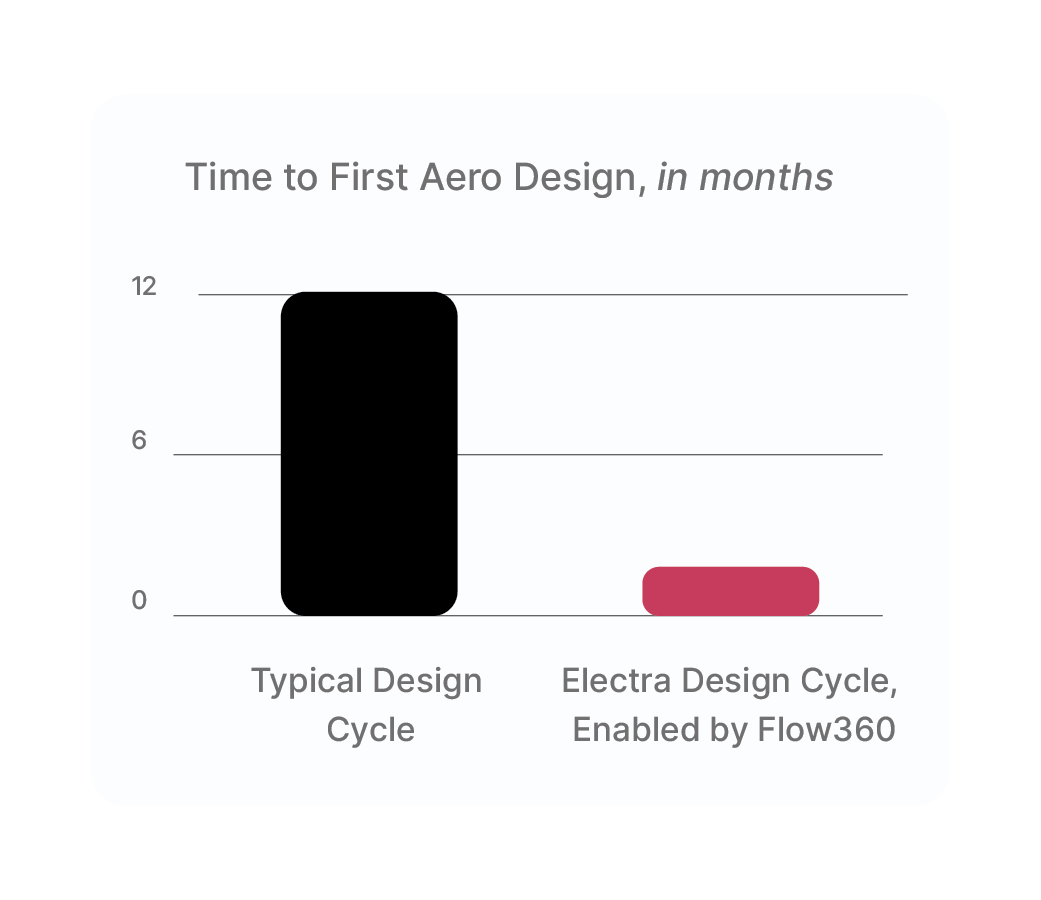
You can read more about this partnership in a paper co-authored by Flexcompute and Electra. If you’d like to learn how Flow360 enables rapid iteration in aero design, reach out to us at info@flexcompute.com and follow us on LinkedIn.